Cuando necesitamos controlar cargas de manera variable, es decir, atenuando o incrementando su régimen de trabajo, de manera habitual se recurre a la modulación por ancho de pulsos (PWM, Pulse-Width Modulation). El control de velocidad de motores y la intensidad de iluminación incandescente (o de LEDs) son las aplicaciones por excelencia para el PWM. Pero, ¿qué es el PWM? ¿Y el IRFZ44N? En este artículo vamos a ver la forma más eficiente de controlar la velocidad de un motor o la intensidad de un grupo de luminarias con un transistor que no debe faltar entre los componentes esenciales de un experimentador como tú.
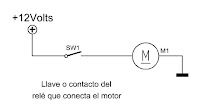
Una de las técnicas más efectivas para conectar o desconectar una carga a una fuente de energía eléctrica ha sido siempre la utilización de simples llaves interruptoras manuales, o un relé activado por un circuito de control muy sencillo. Utilizar otros elementos para este trabajo (por ejemplo, transistores), acarrean necesidades de cálculos de corrientes a conmutar, tensiones de trabajo, y otras variables que una llave o un relé resuelven sin inconvenientes ni consecuencias. Sin embargo, cuando la aplicación requiere el control variable de una carga, comenzamos a imaginar un reóstato enorme y gigante, capaz de manejar muchos amperios y con la capacidad de disipar grandes cantidades de temperatura. Por supuesto que así no se resuelve la situación sino que se emplea una técnica muy sencilla y práctica llamada PWM.
Pongamos como ejemplo que queremos hacer trabajar a un motor de 12Volts a la mitad de su régimen nominal. Lo primero que a muchos se le viene a la mente es aplicarle 6Volts de alimentación. Sin embargo, en la vida real, un motor de levalunas de coche, o un motor que impulsa una bomba de líquido refrigerante en una maquinaria, que debe tener su temperatura de trabajo controlada, no serían capaces de moverse del modo esperado al actuar de este modo. Muy por el contrario, quedarían inmóviles sufriendo un incremento notable de temperatura al ser atravesados por una corriente que no logra movilizar el eje en rotación debido a la carga que el motor tiene acoplada y debe impulsar. Si en cambio aplicamos por un pequeño lapso de tiempo la tensión de alimentación de 12Volts (la nominal de trabajo del motor del ejemplo), éste comenzaría a girar, o haría el intento de hacerlo, hasta volver a detenerse.
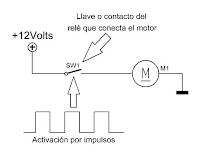
Si aplicamos muchos impulsos en forma reiterada, es decir, conectar – desconectar la alimentación varias veces en un segundo, el motor comenzaría a girar y por la propia inercia del sistema acoplado a su eje, se mantendría en marcha según el régimen de eventos de conexión – desconexión que le apliquemos durante un segundo. El método PWM basa su funcionamiento en este principio. En conectar de manera controlada y durante tiempos ajustables la alimentación, en este ejemplo a un motor, para de este modo poder variar la velocidad sin perder capacidad de tracción, o fuerza. También encontraremos algunos textos que utilicen el término “torque” para esta propiedad motriz. La mejor manera entonces es disponer de una llave o relé controlados de manera inteligente y que conecten – desconecten la carga muchas veces en un segundo. Pero, ¿cuántas veces es lo aconsejable?
En una aplicación de iluminación, si conmutamos (conectamos - desconectamos) la tensión de alimentación menos de 20 veces por segundo, podemos llegar a notar parpadeos molestos a la vista y en el caso de un motor quizás podamos observar o percibir, un accionar muy irregular cual si fuese a los golpes o con impulsos que pueden generar problemas mecánicos a largo plazo, además de entregar una marcha desagradable e incorrecta. Si en cambio elevamos la frecuencia de conmutación por encima de las 50 activaciones por segundo para lograr una marcha estable, caeremos en el problema de comenzar a generar sonidos audibles provocados por el bobinado del motor. Recuerda que el espectro de audición humana se establece entre los 20 ciclos por segundo y los 20 mil. (20Hz. – 20.000Hz.) Por supuesto que el bobinado de un motor no se comportará como un parlante o altavoz tan efectivo como para abarcar toda esta gama de frecuencias con absoluta fidelidad, pero existirán segmentos de resonancia donde algunas frecuencias hagan vibrar los bobinados más que otras, provocando un desagradable sonido que no debiera existir.
Si analizamos este razonamiento, llegamos a la conclusión que para obtener un funcionamiento suave, sin golpes, parpadeos ni sonidos extraños, debemos trabajar con frecuencias superiores a las que un bobinado de motor pueda “resonar”. Estas frecuencias se ubican, en la mayoría de los casos, por encima de los 10Khz. Una vez encontrada la frecuencia apropiada de funcionamiento para nuestro sistema, observaremos que quizás sean demasiadas conexiones en un segundo para la velocidad mínima deseada. Digámoslo de este modo: es probable que el motor gire demasiado rápido y nosotros necesitemos una velocidad menor. Bajar la frecuencia de conmutación es impracticable porque comenzarían los ruidos, entonces, ¿qué opción nos queda?: El PWM. Variar el ciclo de trabajo de la señal conmutada que sirve de activación del sistema. Manipular el ancho del impulso de conexión a la carga.
De este modo, podemos trabajar con frecuencias tan altas como 10Khz. y obtener un ancho de impulso del 1% (o menor) de la señal. A medida que este ancho del impulso comienza a aumentar, la energía promedio que se entrega a la carga también lo hace, pudiendo ser calculada y controlada de manera muy precisa. En el caso de utilizar un microcontrolador, obtendremos mediante su programación, una secuencia de “unos” y “ceros” que respetarán una frecuencia fija pero que pueden tener un ciclo de trabajo variable. Este término, también conocido como Duty, hará variar el ancho del impulso de conexión para obtener así un funcionamiento controlado desde la detención absoluta hasta la marcha a máxima potencia. Para esto, dentro de la programación del microcontrolador, asignaremos una variable al ciclo de trabajo o duty, que será del tipo BYTE y podrá adquirir valores entre 0 y 255. Para un duty igual a cero, el motor estará detenido. Lo mismo que para un valor de 1 o 2. A pesar de ser impulsos enviados al motor que poseen su tensión nominal de trabajo y que se ejecutan a una frecuencia de más de 10Khz., no tendrán el ancho suficiente para entregar la energía necesaria que el motor necesitaría para comenzar a girar, o la luminaria comenzar a encender.
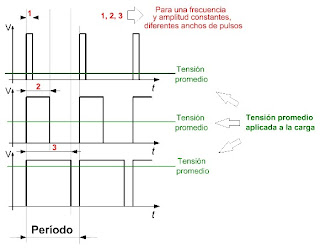
Si en cambio incrementamos el valor de la variable duty a 100, la relación será 100/255 = 0,392 = 39%. Con este nivel de energía aplicada al motor podemos llegar a alcanzar el esfuerzo suficiente como para movilizarlo y mantenerlo funcionando en un régimen aproximado al 40% de la velocidad máxima. Por otro lado, debemos tener en claro que al momento de realizar un programa dentro de un microcontrolador, el desarrollador puede dar marcha al sistema con un duty máximo (255) durante algunos instantes para obtener un arranque a máxima potencia para luego descender de manera suave y progresiva al 40% antes elegido, o también puede hacerlo de manera abrupta, de un instante a otro, aprovechando que no se notará una disminución brusca en la velocidad gracias a la inercia mecánica del sistema acoplado al eje del motor. Para el caso de una luminaria, esta variación brusca no podrá disimularse, pero si el arranque a un duty máximo es lo suficientemente corto, el fenómeno no alcanzará a notarse. De todos modos, en el caso de las luminarias siempre será deseable iniciar con baja potencia para luego incrementarla, es decir, a la inversa de los motores eléctricos. Por lo tanto, el PWM es una herramienta que posee el desarrollador/programador para variar el régimen de trabajo de motores o luminarias con la mayor eficiencia posible.
Para el tipo de conmutación mencionado hasta aquí y para obtener un funcionamiento satisfactorio a una frecuencia tan elevada, una llave mecánica o un relé se vuelven imposibles de utilizar. Es aquí donde hace su presentación el IRFZ44N. ¿Qué es el IRFZ44N? Es un transistor de tecnología MOS-FET (Metal–Oxide–Semiconductor – Field Effect Transistor) que posee destacadas características que lo hacen ideal para este tipo de aplicaciones. Queremos también aclarar que PWM se puede realizar con transistores bipolares (NPN - PNP), con tiristores, triacs, o IGBT según la conveniencia de la aplicación, es decir, el PWM no se hace sólo con un transistor MOS-FET como veremos ahora sino que puedes encontrar aplicaciones que utilizan sistemas electrónicos de conmutación muy variados y como mencionamos antes, ajustables a las necesidades de la aplicación.
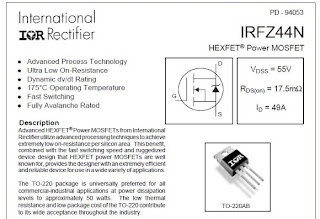
Entre las características más destacadas de este transistor encontramos que es capaz de manejar corrientes de hasta 50 Amperes ofreciendo una resistencia tan baja como 0,017 Ohms. Esto permite un régimen de trabajo extraordinario ya que trabajando al máximo de sus posibilidades no desarrollará una potencia mayor a los 45 Watts. Nada extraordinario para un generoso disipador que pueda irradiar el calor generado por semejante corriente circulando a través del dispositivo. Para que tengas una idea, trabajando con 12 Volts, una lámpara incandescente de 100W consumirá 8,33 Amperes. Es decir, la sexta parte de sus posibilidades extremas y claro está, a 100W, es decir, a la potencia máxima o a un duty de 255.
Una sencilla y práctica explicación del funcionamiento de un transistor MOS-FET puede resumirse a comprender el comportamiento de la circulación de corriente dentro del transistor. Al aplicar una determinada tensión sobre la compuerta, puerta o Gate (positiva respecto a GND), se genera dentro del transistor un campo eléctrico que permite la circulación de corriente entre el terminal identificado como Drain y el terminal Source. Tan simple como eso. Al aplicar tensión al Gate, el campo eléctrico aporta huecos o lagunas, hecho que favorece y activa la circulación de electrones entre Drain y Source. Cuando la tensión en Gate se interrumpe o se coloca a un bajo potencial, la corriente entre Drain y Source se interrumpe. Tenemos de este modo una llave electrónica comandada por tensión (no por corriente, atentos a este punto) que no tendrá inconvenientes en conmutar a frecuencias tan altas como las que necesitamos para controlar una carga.
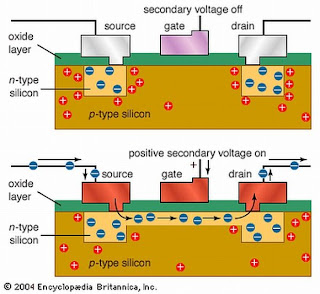
La tensión mínima de Gate para que el transistor comience a conducir (según su hoja de datos que encontrarás al final del artículo) está ubicada entre 2 y 4 Volts mientras que la máxima tensión aplicable respecto al terminal Source, es de 20 Volts. Con 10 Volts de tensión sobre el Gate el transistor alcanza la mínima resistencia entre Drain y Source. Si se sobrepasa la tensión Vgs (tensión de Gate respecto a Source) máxima de 20 Volts el transistor se rompe y si no se alcanza la tensión mínima de 2 a 4 Volts, el transistor no entra en conducción. Una situación a destacar es que si trabajamos siempre con 5 Volts, estaremos sobre el límite de activación del transistor, mientras que si trabajamos con mayor tensión sobre el Gate lograremos un mejor desempeño con menor disipación de calor al ofrecer menor resistencia a la circulación de corriente entre Drain y Source.
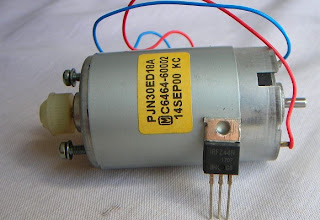
Otro de los detalles importantes a considerar en un diseño que utilice PWM con un MOS-FET es el manejo de los tiempos y las formas de los flancos de subida y bajada de la señal aplicada al Gate. No respetar con fidelidad la forma de onda con la que se debe activar el Gate de un MOS-FET puede llevarte a disipaciones anormales de temperatura y funcionamientos al límite de los márgenes de seguridad térmica. El circuito mostrado permite un óptimo trabajo del transistor. En cambio, si la alimentación desciende a 5 Volts (puede suceder por diseño) la resistencia de Gate debe bajar a valores entre 2,2 y 5 Ohm ya que la tensión de activación del Gate estará al límite de los valores mínimos de operación. Recuerda observar siempre la hoja de datos para lograr un diseño apropiado.
Asignatura: E.E.S
Ver: http://deividorozco.blogspot.com/